¿Cómo lo puede ayudar KERN IoP en su objetivo de entrar al mundo de la Industria 4.0?
- Dr.-Ing. Miguel Garzón
- Aug 19, 2021
- 2 min read
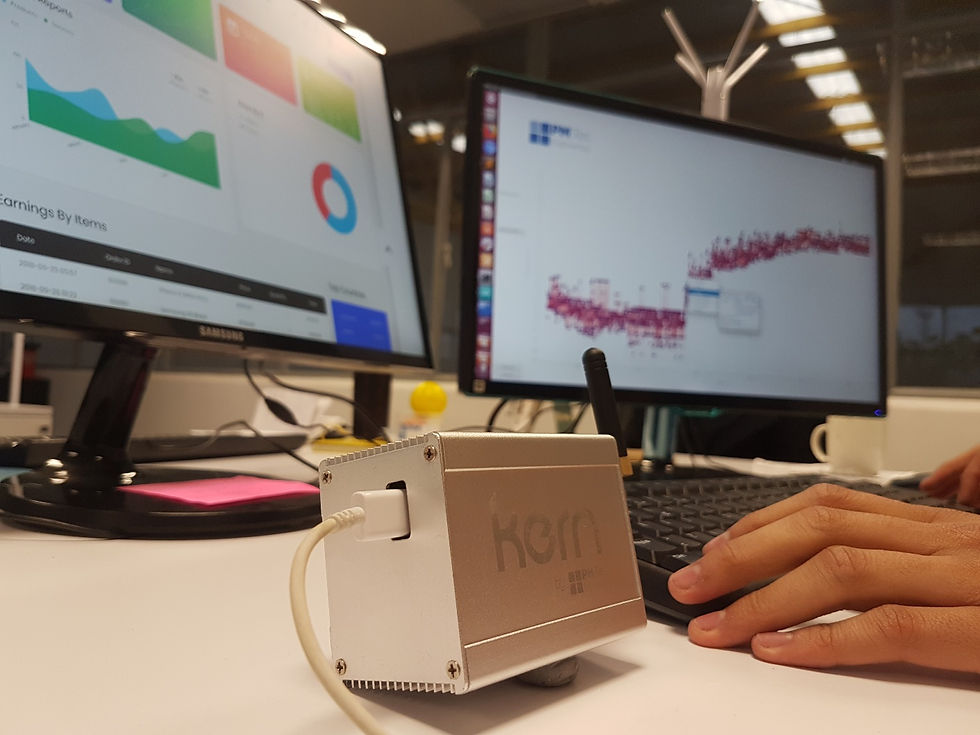
Si se quiere lograr los objetivos propuestos en la filosofía de la Industria 4.0 es necesario que todos los datos clave para un proceso sean adquiridos, digitalizados y estructurados. En etapas iniciales de la implementación de procesos industriales de monitoreo es importante obtener datos sobre la cantidad de partes (y en lo posible, cantidad de partes buenas). En el caso de procesos de manufactura, es crucial adquirir horas reales de producción (tiempo de uso del husillo), de las que se pueden calcular tiempos de montaje y configuración, tiempos muertos (errores, reparaciones, máquina sin pedidos de producción, etc.). Otros datos por recolectar pueden ser el tipo de herramental utilizado, desgaste, horas iniciales de uso, tipo de falla al final de su vida útil, etc. El objetivo de recoger estos datos es el aumento de la productividad, incrementar la ocupación de la máquina, minimizar los tiempos de montaje y tiempos muertos, además de entender el porqué de un incidente con la máquina. Su utilidad para planeación de reparaciones y de mantenimiento es también muy alta dado que se pueden determinar las horas reales de operación de los componentes críticos. Finalmente, tener un histórico de datos de toda la cadena de producción permite hacer cálculos de costos mucho más realistas y comenzar a modelar el comportamiento del proceso, basado en sus variables de entrada y así predecir posibles efectos sobre las piezas fabricadas.
Los sistemas KERN IoP le ofrecen la capacidad de entregar todos estos datos a un sistema de manejo y análisis de información de producción tipo MES (Sistemas de Ejecución de Manufactura, por su abreviatura en inglés), reduciendo la cantidad de información tomada y administrada por los trabajadores manualmente . KERN IoP ayuda en la generación de cultura de administración del conocimiento de las fábricas inteligentes haciendo que los miembros de las empresas tengan clara la importancia de conservar estos datos para su análisis y futura toma de decisiones informadas.

El sistema KERN Monitor permite la visualización en tiempo real de los datos adquiridos para que se puedan aprender las razones por las que suceden los cambios en productividad y calidad. Tener los datos a la mano y ganar conocimiento sobre la influencia de los diferentes parámetros de producción sobre el resultado final, permite obtener una mayor flexibilidad a la hora de tomar decisiones en caso de que ocurra algún cambio inesperado. De esta manera sucede algo radical en las empresas: la organización de cada proceso, dependiendo de sus condiciones propias, elimina la necesidad de una planeación rígida y estricta que también consume tiempo. Aún más, el tipo de trabajo puramente rutinario que ha evitado que muchos de los operarios de planta usen su capacidad analítica para resolver problemas, ahora permite que tomen decisiones durante el proceso porque cada vez más se pueden predecir las consecuencias de las variaciones de los diferentes parámetros. De esta manera se empoderan para generar soluciones alternativas que hacen más eficiente la producción, aumentando así el conocimiento interno de las compañías y, por tanto, agregando valor a la cadena productiva.
Comments